In the world of industry and manufacturing, welding stands as a cornerstone, essential for constructing everything from towering metal structures to intricate machinery. The integrity and strength of these creations hinge on the quality of the welds, making the process not just important but critical. This level of importance elevates the need for precise, reliable welding tools that ensure every weld is executed with perfection. In this article, we will explore the key factors that make quality welding equipment indispensable and how it directly impacts the success of industrial projects.
Fundamental Understanding of Welding
Welding is a fundamental fabrication process that utilizes intense heat to melt and fuse parts together, creating a solid bond between them. During this process, a filler material is introduced to the joint, forming a molten pool that solidifies into a robust and durable connection as it cools. This technique is integral to the construction and repair of countless objects, from large-scale industrial structures to delicate machinery. At The Edge WA, the importance of quality welding equipment is paramount, as it serves as the indispensable toolset for achieving precise and strong welds.
Quality Equipment is Paramount
Having high-quality welding equipment is not just a recommendation—it’s an absolute necessity for any serious welding operation. The caliber of the tools and machinery used directly impacts the efficiency, precision, and safety of the welding process, making the difference between a flawless outcome and a potentially hazardous one. In lean, efficient operations, the need for top-tier welding tools becomes even more critical, as every aspect of the workflow depends on the reliability and performance of the equipment.
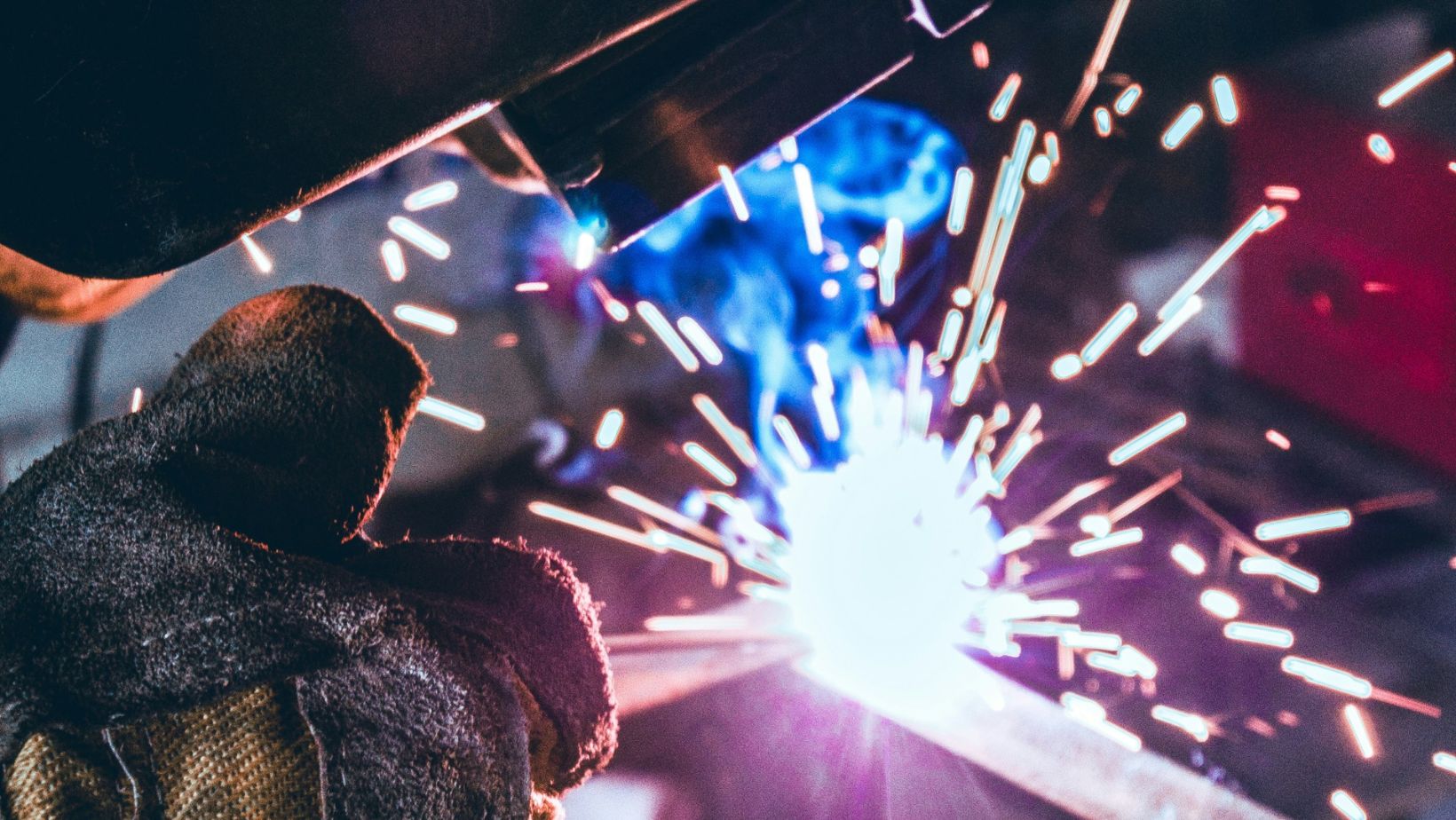
When quality welding tools are employed, the benefits extend beyond just the immediate task at hand, fostering long-term success through reduced downtime, consistent results, and enhanced worker safety.
Precision and Efficiency
Top-quality welding equipment plays a crucial role in enhancing both precision and efficiency, which are essential for the success of any operation. Unlike inferior alternatives, these high-grade tools enable the creation of exact welds that consistently meet stringent specifications, eliminating the need for excessive rework or adjustments. This level of precision not only ensures that the final product adheres to the highest standards but also improves repeatability, which is vital for maintaining consistent quality across multiple projects. The result is a significant reduction in both costs and the time required to complete a job, as fewer resources are wasted on corrections and delays.
Durability and Longevity
High-quality welding equipment is engineered for longevity, providing durability that far surpasses what low-quality alternatives can offer. Built to withstand the rigorous demands of industrial use, this equipment continues to perform reliably without the constant need for maintenance or frequent replacements. This robust construction not only ensures that the tools can handle the most challenging tasks but also minimizes downtime, keeping operations running smoothly. By investing in such durable equipment, businesses can significantly reduce their total cost of ownership over time, as the initial investment is offset by fewer repair costs and a longer lifespan.
Safety Considerations
Safety is of paramount importance in welding, where the risks of injury or accidents are ever-present. High-quality welding equipment plays a crucial role in safeguarding workers by ensuring that operations are conducted with the utmost care and precision. Reliable gear, such as helmets, gloves, and protective clothing, is essential for shielding workers from hazards like sparks, heat, and harmful fumes. When these protective items are paired with dependable welding machinery, the likelihood of accidents or injuries is greatly minimized, fostering a safer working environment. Investing in top-quality safety equipment is not just about compliance—it’s about protecting the well-being of workers and maintaining a secure, efficient workplace.
Quality Assurance and Standards
High-quality welding equipment adheres to established standards and guidelines that ensure its performance, reliability, and safety.
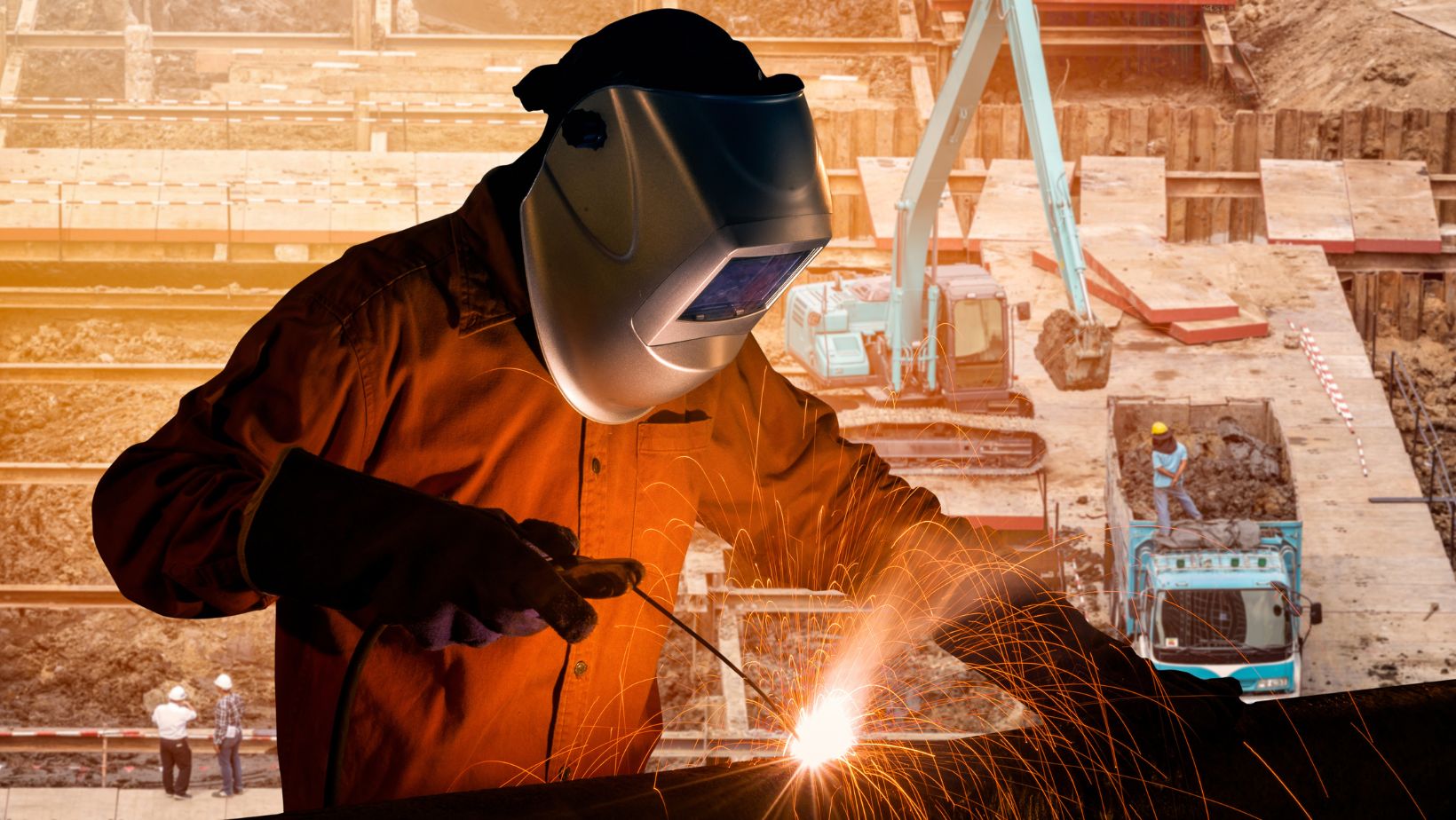
Products from reputable manufacturers are often certified with marks like the CE symbol, which signifies compliance with the stringent safety, health, and environmental requirements of the European Union. This certification not only provides assurance that the equipment meets rigorous quality standards but also reflects the manufacturer’s commitment to producing tools that are safe for use in various industrial environments.
The Key Role of Training and Support
Quality welding equipment is frequently accompanied by robust support and comprehensive training resources, which are invaluable for ensuring optimal use and safety. These training programs help welders understand the full capabilities of their tools, allowing them to maximize efficiency and precision in their work. Moreover, proper training enhances safety by teaching best practices and proper handling techniques, reducing the risk of accidents.
Conclusion
As we navigate the realm of industrial welding, it becomes ever so clear that quality welding equipment is of pivotal importance. In its role to promote precision, efficiency, durability, safety, and compliance with standards, quality equipment becomes an indispensable factor. To successfully rise to the challenge of this demanding field, you must adequately equip yourself. This means investing in quality welding equipment that you can rely on to perform optimally, coupled with practical training and support from trusted institutions like The Edge WA. After all, a job well welded, is a job well done.